How to maintain electric sightseeing car
As people increasingly enjoy the convenience and quickness brought about by the material, travel to major scenic spots is no longer the only way to choose to hike on foot. In contrast, more choices of electric sightseeing car to experience the mobile tour mode . Not only does it make you feel comfortable, but you can also enjoy more scenery in a tight sightseeing time. Therefore, for the scenic spot, the daily maintenance and maintenance of the electric sightseeing tourist vehicle must be done enough homework, so as to undertake the tourist sightseeing mission on weekdays and holidays.
First, the core component of the electric tour car is the battery for energy supply, so the maintenance of the battery should be placed in the first place. According to the principle of battery-powered performance, when driving, you should drive as evenly as possible, to avoid sudden changes in the speed of the current during rapid braking or rapid acceleration, thereby damaging the relevant physical characteristics of battery power. The battery is charged with the use of charge, grasp the specific charging time, to prevent the battery overcharge heat. According to the driving conditions of each electric tourist car, different charging frequencies are used. Periodically, according to the operation manual, relevant inspections shall be carried out on the storage battery to check for any leakage or leakage of electricity and instability of the power supply.
Second, due to the stable nature of the electric tour tourist vehicle requirements, for four or more rounds of electric sightseeing tour car tires should be done in a timely manner regular inspections. Formed the habit of detecting the tire pressure frequency of the tire. Avoid the phenomenon of unbalanced cars and excessive power consumption caused by uneven tire pressure.
Third, electric sightseeing car to facilitate the upper and lower tourists are mostly doorless design, the car will generally be equipped with safety rods, safety bolts, safety chains and other protective equipment. The safety of these safety devices should be checked regularly to check whether the safety devices are complete or not. Check for looseness and breakage. To avoid accidents when driving on some scenic complex roads.
The above three points are only general considerations for the power, stability, and safety of electric sightseeing vehicles . There are still many details that need to be paid attention to in actual use and maintenance. There is an opportunity to discuss with them later.
Stamping Parts:
The processing method for stamping and forging are plastic processing (or pressure processing), forging stamping blank collectively. Is hot-rolled and cold-rolled steel sheet and strip. The world of steel, 60 ~ 70% is the plate, mostly made by stamping products. Automobile body, chassis, tank, radiator, boiler drum, vessel shell, electric machine, electric iron core silicon steel sheet are stamping processing. Instruments, household appliances, bicycles, office machinery, household utensils and other products, there are a large number of Stamping Parts stamping. Is powered by conventional or special punching equipment, make sheet metal in the mold directly affected by the deformation force and deformation, thus A certain shape, size and performance of the product parts production technology. The sheet metal, mold and equipment are the three elements of stamping. Temperature divided by stamping hot stamping and cold stamping. The former is suitable for high deformation resistance, sheet metal plasticity is poor; the latter was carried out at room temperature, is commonly used in stamping method the sheet metal plastic processing. It is (or pressure processing) one of the main methods, but also forming part of materials engineering. Stamping mold called stamping die, or die. The die is the material (metal or non-metal) batch processing into the special tool stamping. Die is of vital importance in the in the press, did not meet the requirements of the die, it is difficult to carry out production batch stamping die; no advanced, advanced stamping process can not be achieved. The stamping process and die, stamping equipment and stamping materials to constitute three stamping processing Only when they combine with each other can they get the stamping parts.
WHY Stamping:
Stamping parts and castings, forgings, a thin, uniform, light, strong character. Stamping can be produced from other methods is difficult to manufacture with stiffeners, stamping parts stamping rib, rolling or burring of the workpiece, to improve its rigidity. Because of the use of precision molds, workpiece precision, and high repetition accuracy, specifications, can punch a hole nest, boss. Cold stamping generally no longer cutting machining, or only a small amount of cutting. The hot stamping precision and surface state below the cold stamping, but still better than the casting, forging, machining less.
(1) Stamping processing is of high production efficiency, convenient operation, easy to realize mechanization and automation. This is because the stamping dies and stamping equipment rely on to complete the processing, ordinary press trips per minute up to dozens of times, high pressure per minute up to hundreds or even thousands of times, and each press stroke you may get a red piece.
(2) The stamping die ensure the dimension and shape precision stamping parts, and generally do not damage the surface quality of stamping, and die life is generally longer, so the stamping quality, good interchangeability, "as like as two peas" feature.
(3) Stamping can press the processing size range is large, complex shape parts, such as a small clock stopwatch, large car rails, covering parts, stamping and material hardening effect of cold deformation, punching strength and stiffness are higher..
(4) Stamping generally without cutting scrap generated, material consumption is less, and no other heating equipment, which is a kind of material saving, energy saving and processing, lower the cost of stamping parts.
Category:
Stamping is mainly according to the process of classification, can be divided into separation process and the forming process of two categories. The separation process also known as blanking, its purpose is to make the stamping parts along the contour line must be separated from the sheet, and guarantee the quality of the separation section (Table 1). The forming process is designed to make sheet metal in broken slab under the condition of plastic deformation, the workpiece into the required shape and size. In the actual production, often a variety of integrated process applied to a workpiece. The blanking, bending, shear, tensile, bulging, spinning, correction is the main stamping process of several.
Mainly speaking,based on the three different material,we can make steel stamping farts,copper alloy stamping parts and aluminium alloy stamping parts.
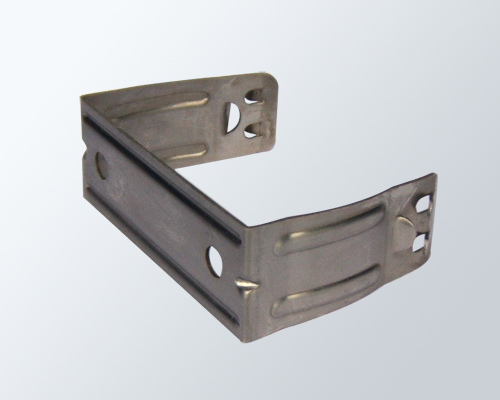
Stamping Parts
Stamping Parts,Steel Stamping,Copper Stamping,Aluminium Stamping
VESTA Motoring Ltd , https://www.vesta-industry.com